Engineering
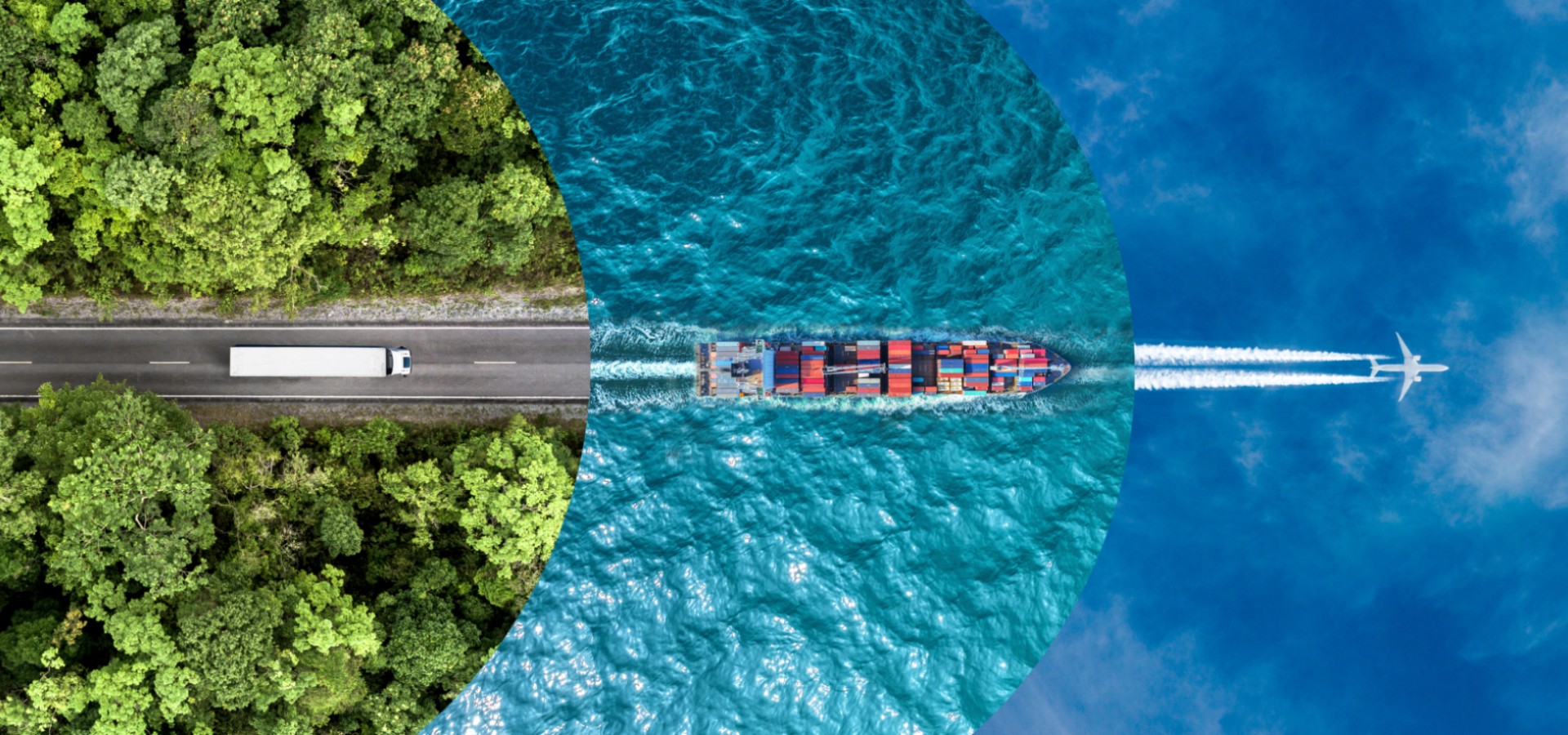
Eminox flexible, innovative engineering
Eminox design and manufacture emissions aftertreatment systems with technologies to help optimise engine efficiency. Our control systems monitor changes in pressure, temperature and NOx to adjust aftertreatment operation for optimum performance. We provide a flexible approach to deliver standard and bespoke emissions components and complete solutions for emerging exhaust aftertreatment applications.
Our dedicated project engineering function has strong design and development capabilities for supporting customers in a wide variety of applications including power generation, marine, on-road, non-road mobile machinery (NRMM) and rail, therefore, delivering solutions that ensure your applications meet the latest global emissions regulations.
The Eminox new product introduction (NPI) process includes complete engineering and design services from concept, in-house evaluation and modelling, prototyping, verification and homologation services.
Our global facilities are designed to manufacture your products with in-house quality assurance and a dedicated production cell, which can be adapted to meet your volume requirements. Through our collaboration and communication with your programme team during the full turn-key service, we deliver technologies for a greener planet; which meet your programme timescales and budget.
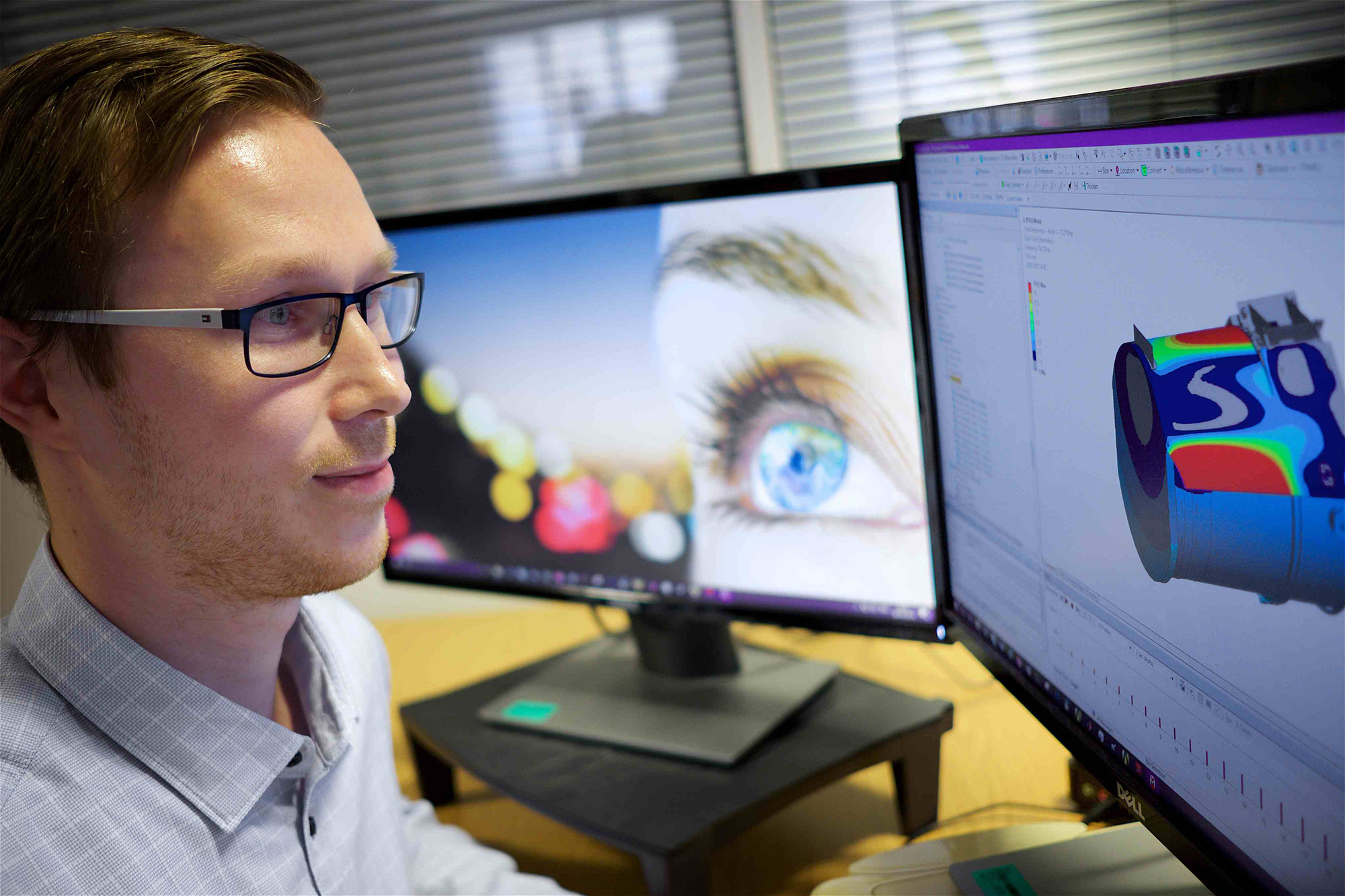
Our approach
The Eminox engineering team conduct exploratory research to better understand the markets you operate in and enable us to develop new technologies aligned with improving air pollution by meeting global emissions standards.
We execute these technologies within platform and project developments from our 7,000m2 modern UK headquarters and manufacturing facility, in Lincolnshire, as well as utilising proven technologies to develop new bespoke products and market solutions; manufacturing from our 5,700m2 Slovakian manufacturing, in Svit.
Working together with your team ensures we meet your requirements to achieve your specified emissions regulations.
We implement Original Equipment Manufacturers (OEM), Retrofit and Aftermarket programmes through a full turn-key service. This ensures we maintain the quality of every project requirement, keeping costs aligned with agreed budgets and delivering emissions control solutions which meet global standards.
By understanding the demands of both on-road and non-road applications, our engineers can transfer product development processes between OEM and retrofit projects, providing cost-effective and rapid responses to your business.
Our engineers use the latest computer aided engineering (CAE) tools, including Computer-Aided Design (CAD) CATIA V6 (3D Experience), Computational Fluid Dynamics (CFD) and Finite Element Analysis (FEA).
Prototypes and testing
We design for manufacture and our in-house, experienced prototype manufacturing team deliver cost-effective, quality prototype systems by working alongside our engineering and testing teams.
The Eminox test house, engine test cell and LMS test laboratory is used to conduct acoustic and vibration testing. Our durability cell enables cold flow testing on our cold fatigue rig, hot durability testing and analysis of prototypes using our hot flow and shake rigs; all to achieve optimal design for manufacture.
Additionally, we collaborate with reliable external partners, to support our drive to deliver technologies for tomorrow whilst bridging the gap to a zero-emissions future; ensuring we provide an emissions control solution for your project now.